Facing bricks
References of the ICS business unit can be found here
COROBRIK, Driefontein - KELLER implements one of the largest brick plants in sub-Saharan Africa
The new plant, which is known as "Kwastina" - Home of the Brick, will produce 105 million extruded first-class facing bricks per year for the South African market and the market of its neighbouring countries. A so-called 'greenfield project' was built close to the existing plant with a new shaping plant, a new fully automatic wet side and a setting plant for direct setting, two tunnel dryers followed by two tunnel kilns and a new unloading and packaging equipment for dispatch packs without pallets.
This project takes a new path in the economical and ecological production of bricks in South Africa. In this way, the energy consumption could even be below the guaranteed consumption value. Thanks to the precision in handling and process control, all products can be manufactured safely and product changes can be made easily.
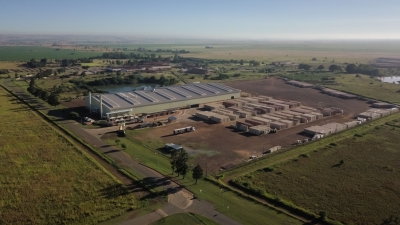
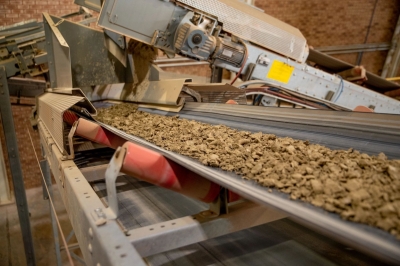
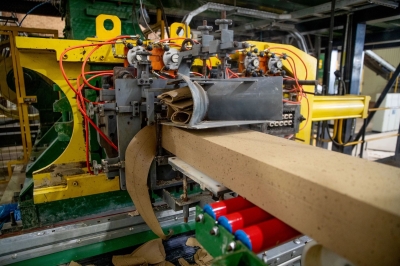

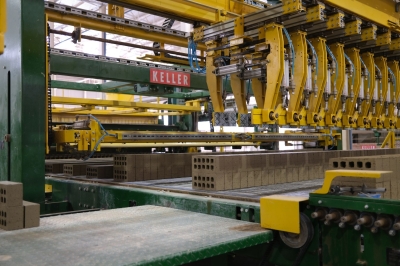
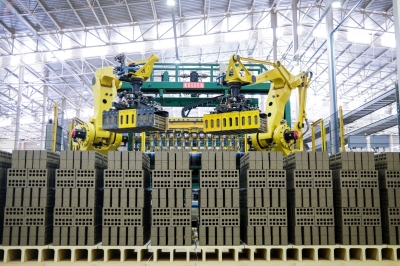
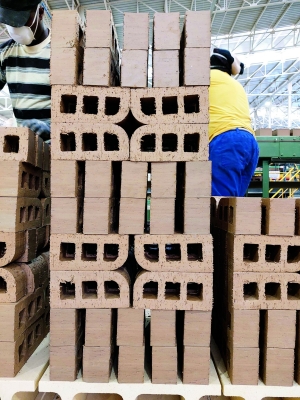
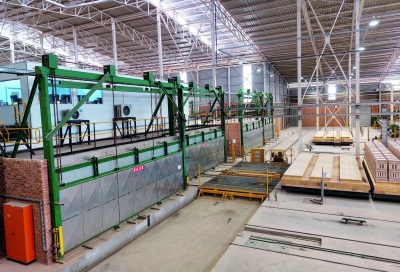
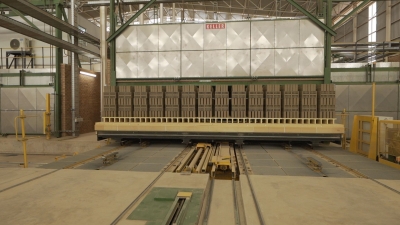
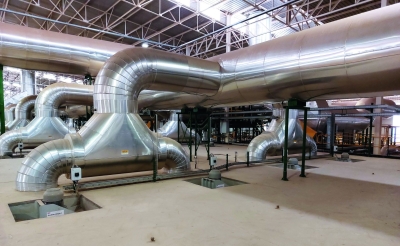
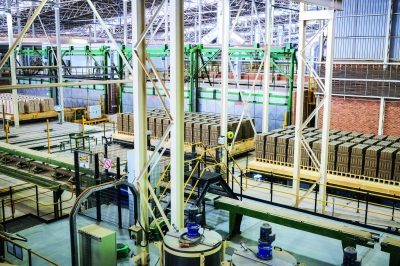
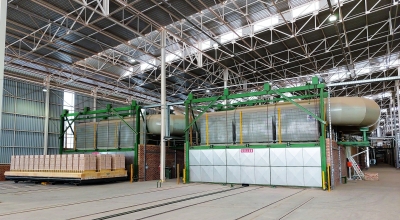
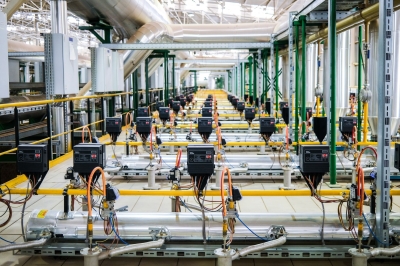
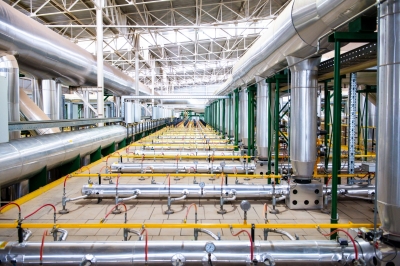
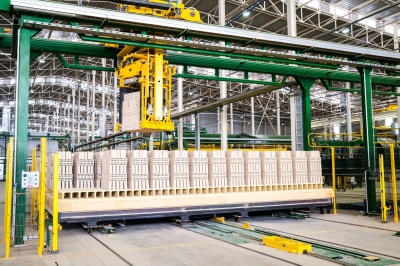
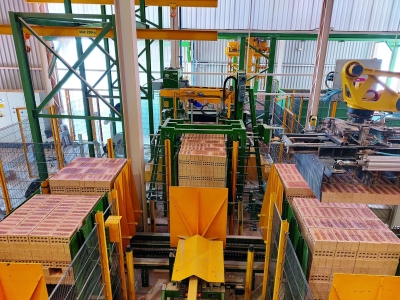
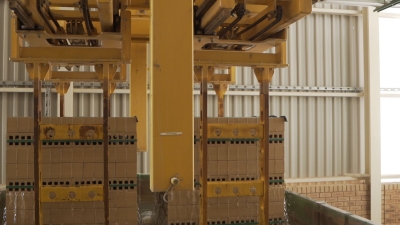
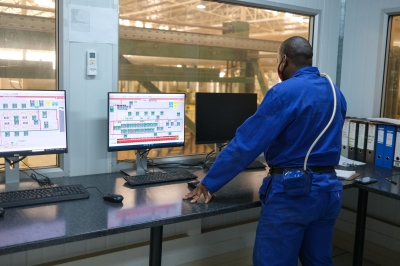
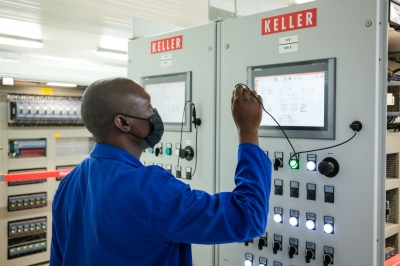
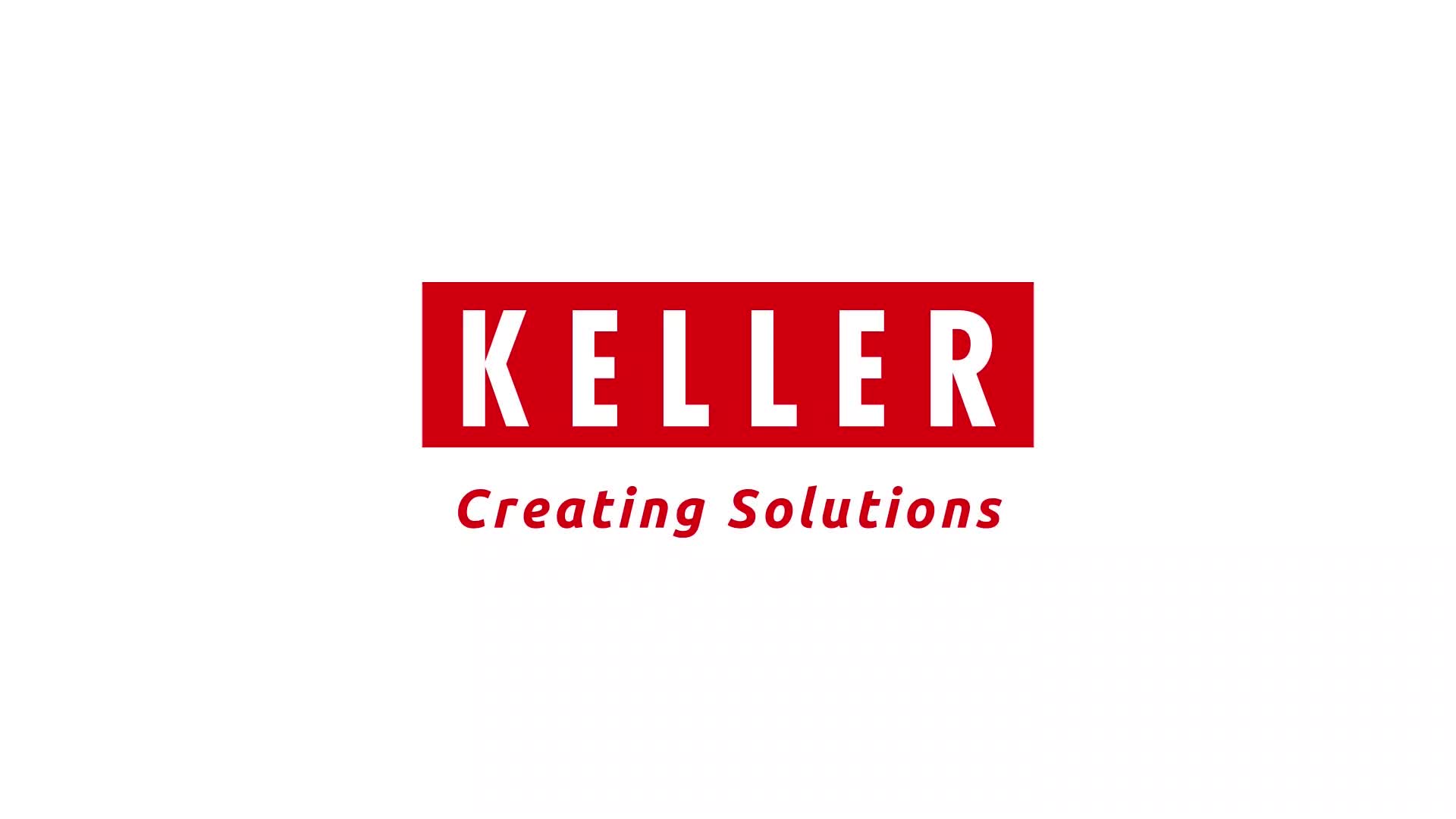

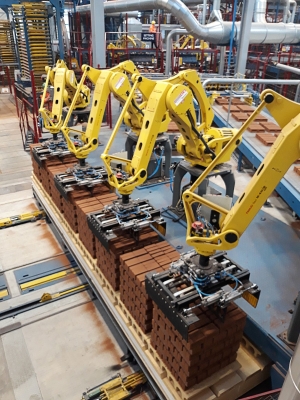
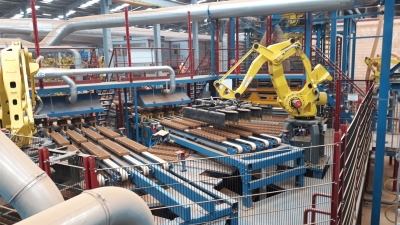
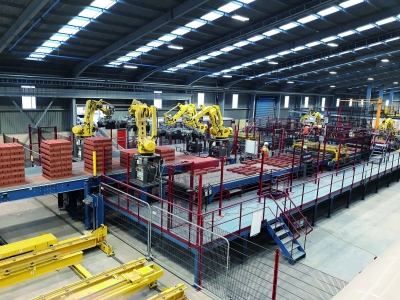
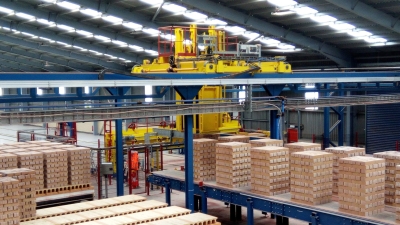
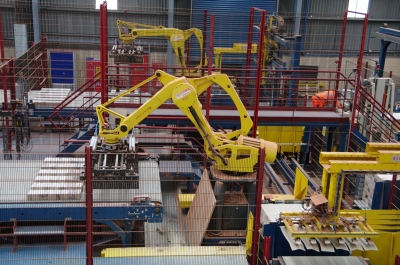
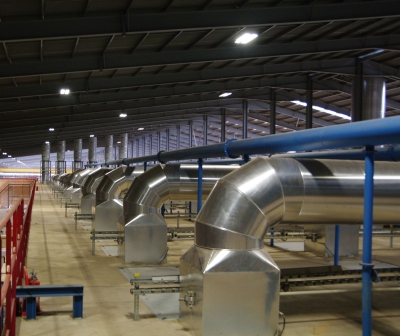
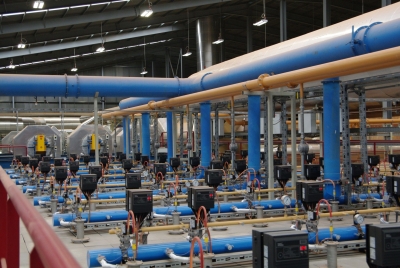
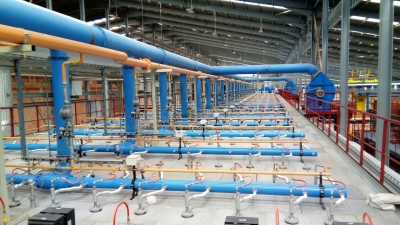
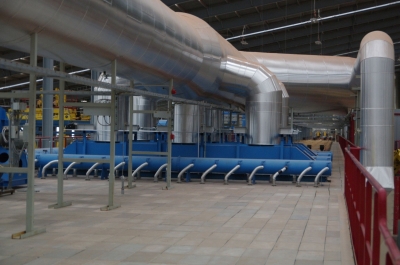
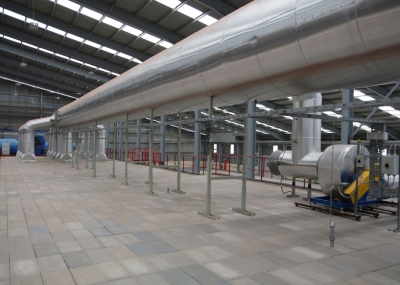
Ibstock Brick, Leicester - KELLER delivers one of the world's most modern facing brick plants to England
The new plant will produce 100 million soft mud bricks per year in a wide range of colours and sizes in line with customer requirements. The scope of supply begins with the take-over of the green products on pallets and the fully automatic loading of the newly developed tunnel dryer cars. The wet and dry side, the setting plant, the unloading equipment and the palletless packaging are fully automatic.
Chamber dryers are usually used in the production of soft mud bricks. Based on the further developed tunnel dryer cars and the dryer with horizontal slot nozzles developed by KELLER, Ibstock Brick was immediately convinced of the advantages of the KELLER tunnel dryer.
The tunnel kiln with upstream holding room is also designed for continuous 24/365 operation and produces an average of 16 tunnel kiln cars per day.
The entire plant is equipped with a Siemens-based S7-TIA control system and the K-Matic software developed by KELLER. Thus, best product results with lowest energy consumption could be realized already after a short time.
Chamber dryers are usually used in the production of soft mud bricks. Based on the further developed tunnel dryer cars and the dryer with horizontal slot nozzles developed by KELLER, Ibstock Brick was immediately convinced of the advantages of the KELLER tunnel dryer.
The tunnel kiln with upstream holding room is also designed for continuous 24/365 operation and produces an average of 16 tunnel kiln cars per day.
The entire plant is equipped with a Siemens-based S7-TIA control system and the K-Matic software developed by KELLER. Thus, best product results with lowest energy consumption could be realized already after a short time.
COROBRIK, Rietvlei - KELLER builds fully automatic unloading and packaging plant in South Africa
The fully automatic unloading system starts with the unloading of packs from the kiln car. The packs are then de-stacked in layers by industrial robots and divided into individual rows.
After manual sorting, the bricks are formed to packs without pallets and are strapped vertically as well as horizontally.
The required plant capacity was achieved and the quality of the dispatch packs improved. This is particularly noticeable in the case of longer journeys to the end customer.
After manual sorting, the bricks are formed to packs without pallets and are strapped vertically as well as horizontally.
The required plant capacity was achieved and the quality of the dispatch packs improved. This is particularly noticeable in the case of longer journeys to the end customer.
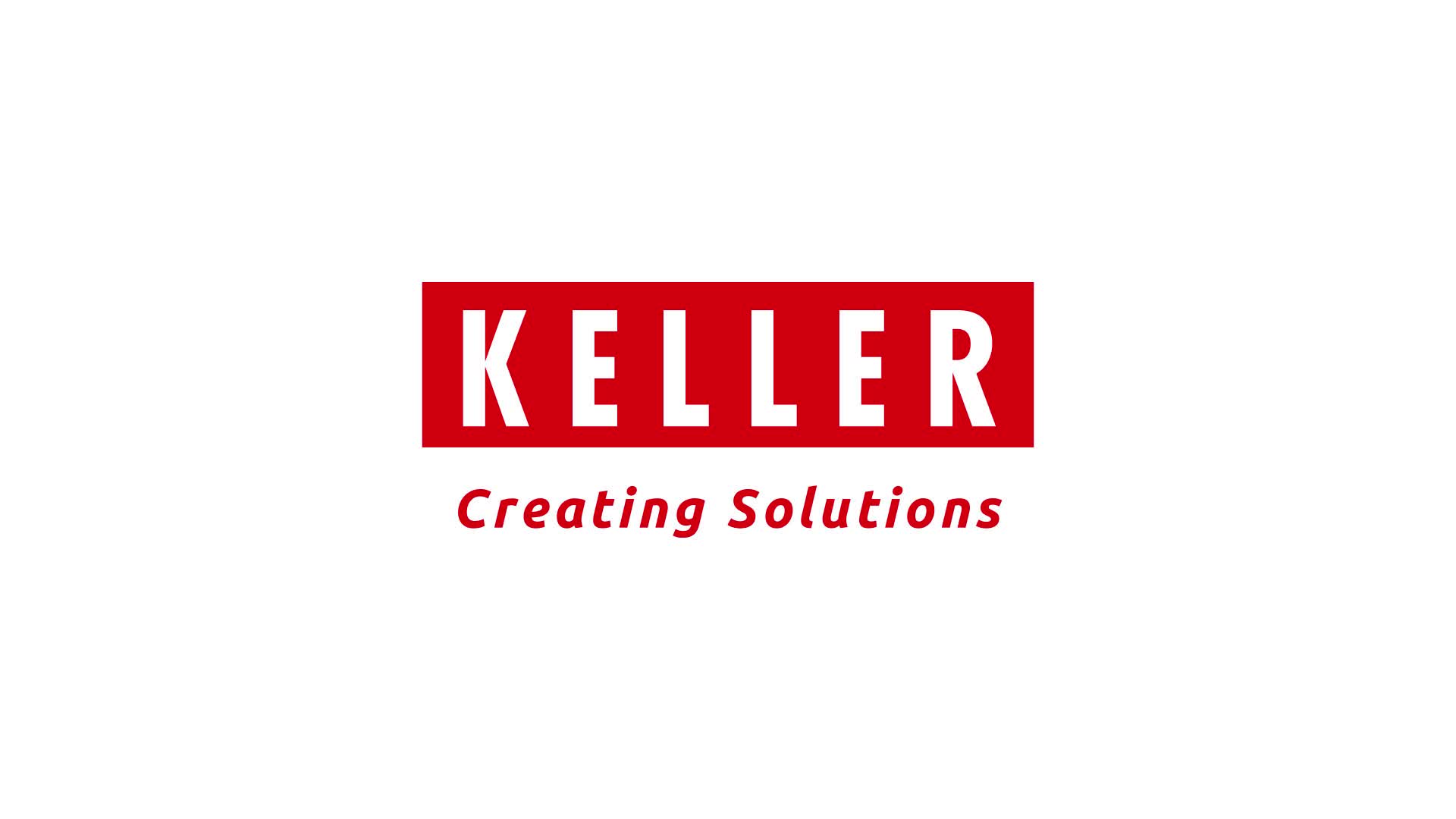
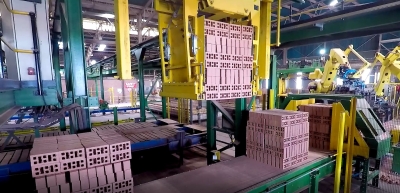
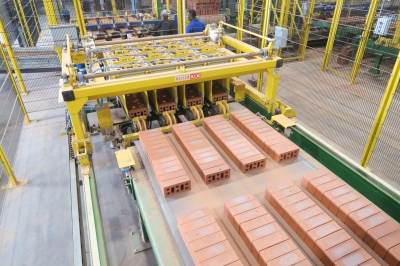
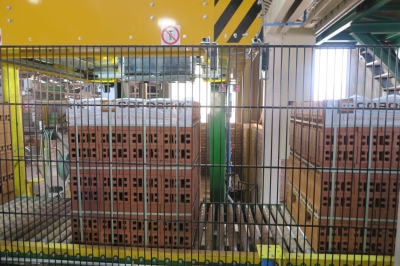
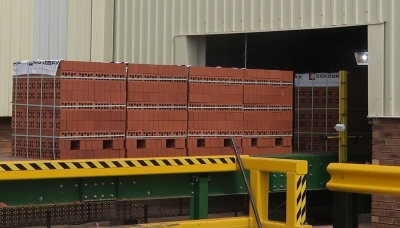
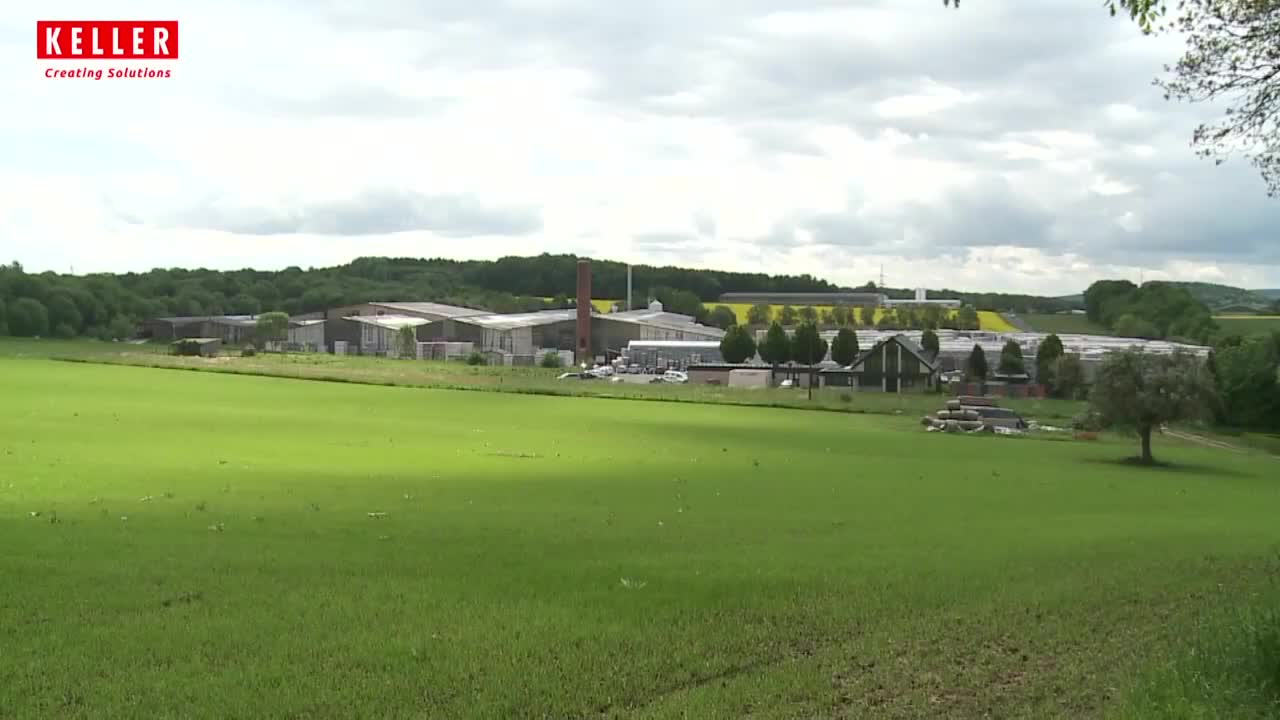
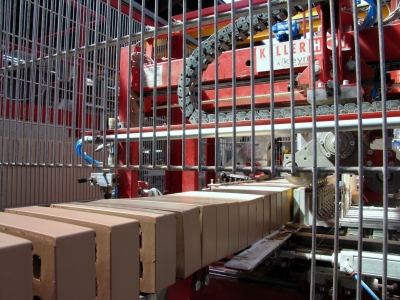
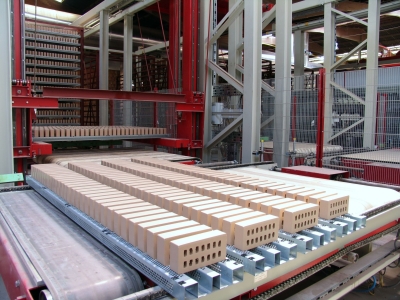
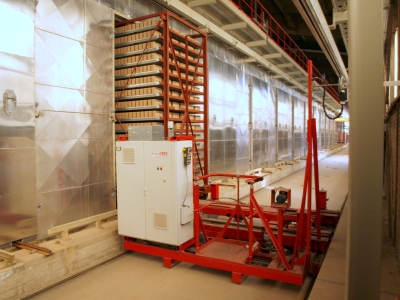
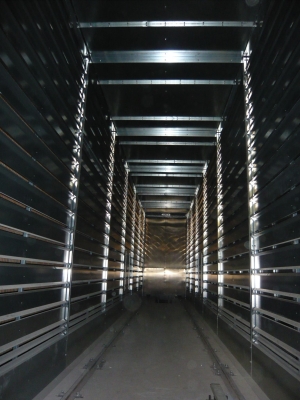
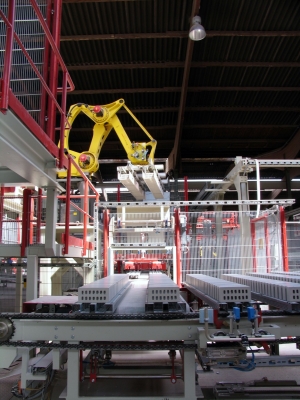
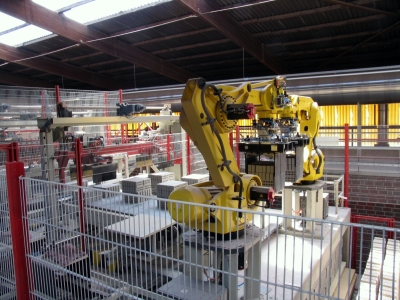
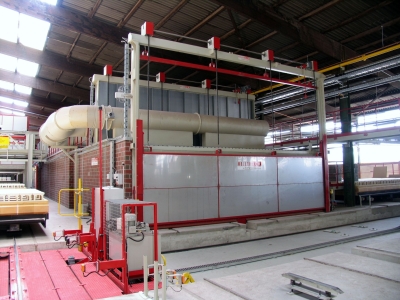
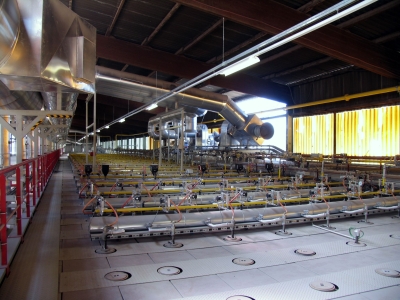
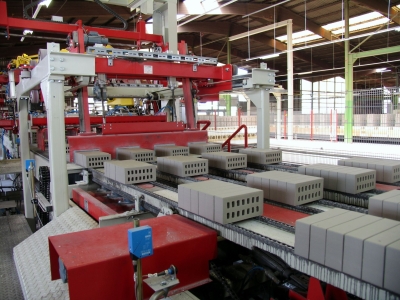
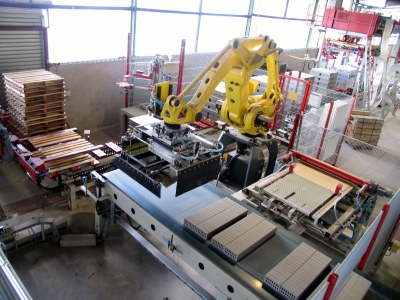
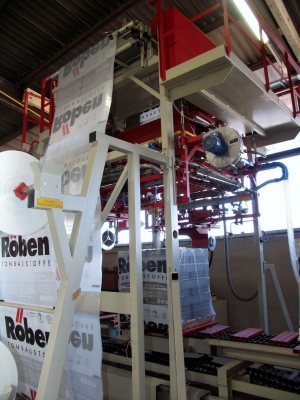
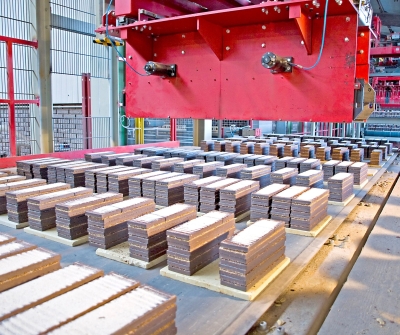

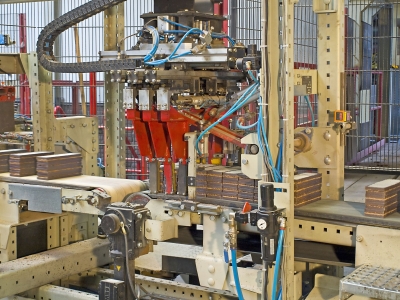
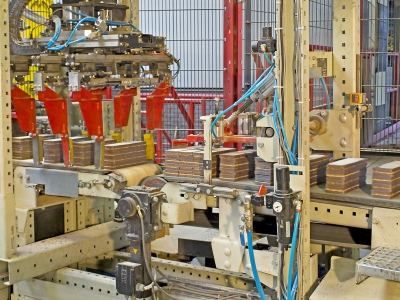
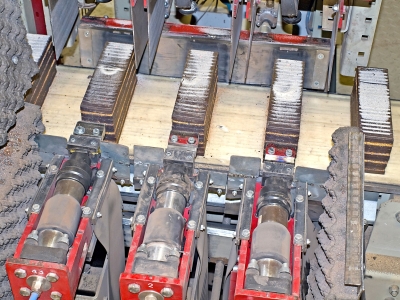
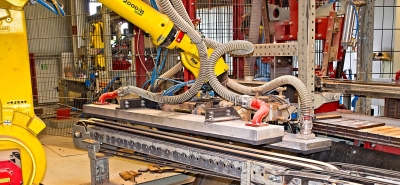
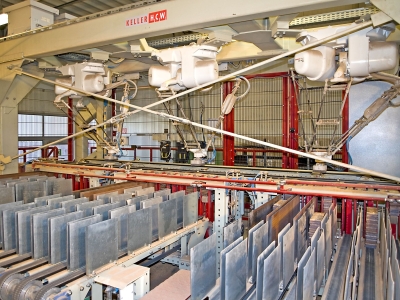
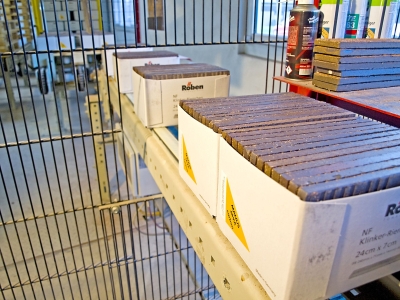
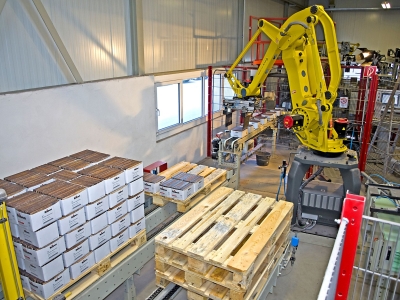
Röben, Bannberscheid - Röben sets new standards in brick production
The plant is capable of producing three different product sizes with three different factory blends at the same time. Highest flexibility and highest quality are the main characteristics of the plant. The product range is diverse: facing bricks, ceramic clinkers, pavers and clinker strips with the typical product characteristics such as durability, frost resistance, accompanied by a large variety of surfaces and colours. The capacity of the plant is 18 million ceramic clinkers and 20 million clinker strips per year.
The production programme includes more than 40 sizes with different surface structures, colours and dimensions.
The size variety places high demands on the machinery: sanding, turning, facing, doubling and crosswise setting are no challenge for the respective machine units. Engobing and glazing of products on bypass lines can be carried out at any time.
The size variety places high demands on the machinery: sanding, turning, facing, doubling and crosswise setting are no challenge for the respective machine units. Engobing and glazing of products on bypass lines can be carried out at any time.