Automation
We embody process-controlled automation
The most important arguments for the automation and process technology by KELLER - KELLER offers you engineering, project management, project completion, assembly and service - all from one source! In addition, a long-standing and extensive know-how - not only in the heavy clay industry - but also in many other industries and future-proof solutions with perfectly coordinated components from the K-matic family.
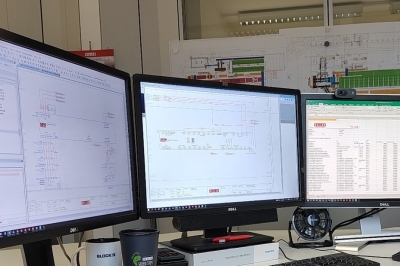
Hardware design
Customer-specific project planning is part of our everyday work
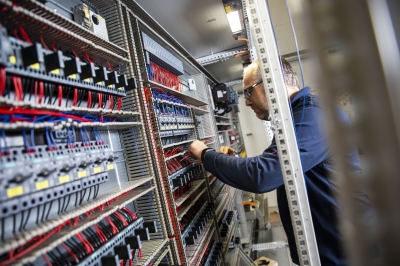
Switch cabinet manufacturing
Individually and precisely tailored
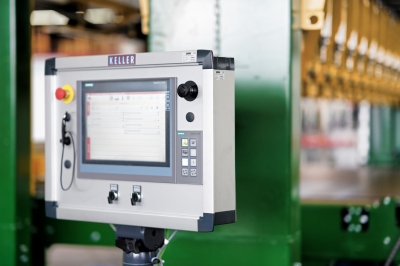
Operation
Operation with a clear view - our visualization on the machine
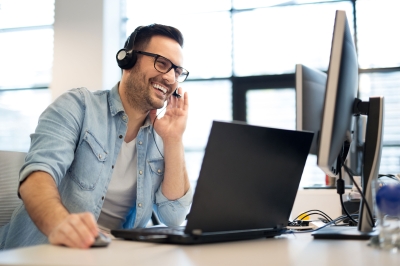
Service
We stay in touch - with you and with your plant
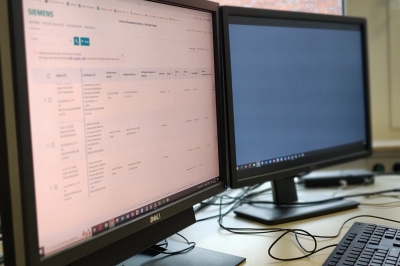
Software design
Customized solutions
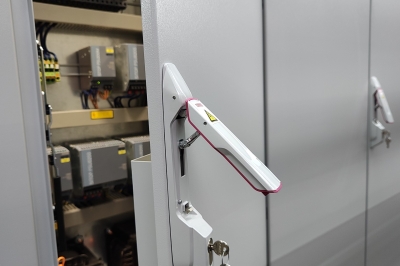
Safety systems
Sure! - our safety systems
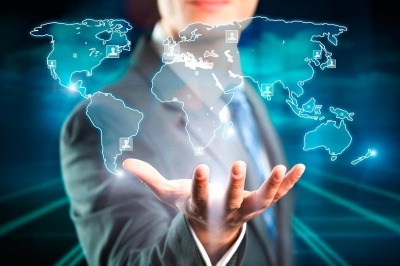
K-matic family
Integrated automation from the field level up to the management level