Herstellerunabhängige IO-Link Schnittstelle für die intelligente Prozessautomation
Einleitung
Derzeit wird das Thema Industrie 4.0 und innovative Maschinenkonzepte in der Automatisierungstechnik umfangreich diskutiert. Grundvoraussetzungen für die durchgängige Vernetzung, volle Transparenz und lückenlose Kommunikation der Analgensysteme bis auf die unterste Feldgerätebene sind intelligente Sensoren. Mit der IO-Link Schnittstelle wurde dazu ein neues, feldbusunabhängiges und herstellerübergreifendes Kommunikationskonzept zur einheitlichen Anbindung von Sensoren und Aktoren an die Steuerungsebene mittels einer einfachen und kostengünstigen Punkt-zu-Punkt Verbindung geschaffen. In dem folgenden Bericht wird die Technologie und Anwendung der IO-Link Schnittstelle vorgestellt.
Industrie 4.0
Industrie 4.0 ist die Verschmelzung der Informationstechnologie (IT) und der Telekommunikationstechnologie zur ITK. Basis ist die Vernetzung von Sensoren, Aktoren und Datenverarbeitung für eine durchgängige Kommunikation bis auf die Ebene der Feldgeräte. Die Vision der Industrie 4.0 erfasst die Digitalisierung, Automatisierung und Vernetzung von allen Anwendungen zur Steuerung des Gesamtprozesses für alle Funktionen, Bereiche und Segmente der Fertigungsindustrie bis hin zu einem wirtschaftlichen Handeln. Getrieben wird diese Transformation primär durch die steigenden Kundenanforderungen bzw. die Notwendigkeit, seitens der Fertigungsunternehmen immer schnellere, dynamischere und individualisierte Kundenwünsche erfüllen zu können. Dies erfordert den Übergang von starren, zentralen Produktionssteuerungssystemen hin zu einer dezentralen Intelligenz bis auf die Feldgeräteebene.
Mit Einführung der Industrie 4.0 in Produktionsprozessen soll eine adaptive Fertigung und Optimierung der einzelnen Prozesse im Echtzeitbetrieb erzielt werden. Entsprechend den definierten Produktions- und Prozesstechniken sollen selbstständig die Materialien und Komponenten ausgewählt werden sowie eine Anpassung und Nachjustierung in Echtzeit möglich sein gemäß dem Motto „Das Produkt steuert die Anlage“. Die Vorteile sind Effizienzsteigerung und Flexibilisierung durch schnellere Reaktion auf höhere Variantenvielfalt, kürzere Umrüstzyklen bei komplexen Produkten, die Fertigung unterschiedlicher Serien oder einzelner Produkte mit derselben Anlage, individualisierte auf Kunden zugeschnittene Produkte sowie die Produktion von Klein- und Kleinstserien zu wettbewerbsfähigen Kosten.
Mit Industrie 4.0 wird das Konzept weg von einer präventiven Wartung- und Instandhaltung von Anlagen hin zu vorhersagbaren Diagnosen und Fernwartung selbst über Werksgrenzen und Standorte hinweg verfolgt. All dies verlangt den Zugriff auf die angeschlossenen intelligenten Datenquellen wie Sensoren oder Aktoren.
Ein Manko der Industrie 4.0 ist der vielfach fehlende Standard und die ungenaue Abgrenzung des Begriffes. Die systemübergreifende Durchgängigkeit und damit weltweite Einsatzfähigkeit braucht einheitliche Rahmenbedingungen für Technologien, Systeme und Prozesse auf Basis internationaler Normen und Standards. Hinzu kommen noch die grundlegenden Vereinheitlichungen von Strukturierungsprinzipien, Schnittstellen und Datenformaten.
Mit Einführung der Industrie 4.0 in Produktionsprozessen soll eine adaptive Fertigung und Optimierung der einzelnen Prozesse im Echtzeitbetrieb erzielt werden. Entsprechend den definierten Produktions- und Prozesstechniken sollen selbstständig die Materialien und Komponenten ausgewählt werden sowie eine Anpassung und Nachjustierung in Echtzeit möglich sein gemäß dem Motto „Das Produkt steuert die Anlage“. Die Vorteile sind Effizienzsteigerung und Flexibilisierung durch schnellere Reaktion auf höhere Variantenvielfalt, kürzere Umrüstzyklen bei komplexen Produkten, die Fertigung unterschiedlicher Serien oder einzelner Produkte mit derselben Anlage, individualisierte auf Kunden zugeschnittene Produkte sowie die Produktion von Klein- und Kleinstserien zu wettbewerbsfähigen Kosten.
Mit Industrie 4.0 wird das Konzept weg von einer präventiven Wartung- und Instandhaltung von Anlagen hin zu vorhersagbaren Diagnosen und Fernwartung selbst über Werksgrenzen und Standorte hinweg verfolgt. All dies verlangt den Zugriff auf die angeschlossenen intelligenten Datenquellen wie Sensoren oder Aktoren.
Ein Manko der Industrie 4.0 ist der vielfach fehlende Standard und die ungenaue Abgrenzung des Begriffes. Die systemübergreifende Durchgängigkeit und damit weltweite Einsatzfähigkeit braucht einheitliche Rahmenbedingungen für Technologien, Systeme und Prozesse auf Basis internationaler Normen und Standards. Hinzu kommen noch die grundlegenden Vereinheitlichungen von Strukturierungsprinzipien, Schnittstellen und Datenformaten.
Grenzen der klassischen Automatisierungstechnologie
Bisherige Vernetzungen und Feldbussysteme sind von den führenden SPS-Herstellern entwickelt worden, die eine systemspezifische Technologie unterstützen und optimal an deren Programmier- und Konfigurationstools angepasst sind. So gibt es mehrere konkurrierende Systeme wie Profibus/ProfiNet (Siemens),DeviceNet und ControlNet (Rockwell Automation), Modbus und CANopen (Schneider Electric), Interbus (Phoenix Contact) oder CC-Link (Mitsubishi Electric) am Markt. Der Typ der eingesetzten SPS bestimmt, welcher Feldbus verwendet wird. Wesentliche technische Unterschiede gibt es bei der Kabellänge, der Anzahl der Datenbits sowie dem Funktionsumfang. Weitergehende Funktionen wie Diagnose, azyklische Übertragung von Bedarfsdaten, Alarmhandling und Querverkehr zwischen den einzelnen Busteilnehmern werden nicht von jedem Feldbussystem unterstützt.
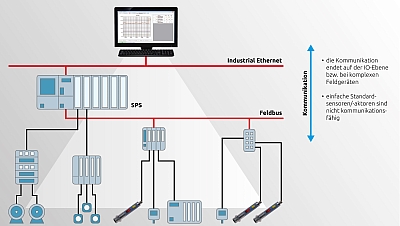
Abb. 1 Klassisches Automatisierungssystem mit begrenzter Kommunikationsmöglichkeit.
Bei der klassischen Automatisierungstechnik endet die Kommunikation bisher auf der untersten Feldbusebene sprich bei den Sensoren und Aktoren (Bild 1). Dort werden vielfach nicht kommunikationsfähige Baugruppen eingesetzt, die sich auf rein analoge oder schaltende Ein- und Ausgangssignale beschränken. Die am Markt verfügbaren Sensoren und Aktoren mit einer digitalen Schnittstelle sind nicht genormt, sondern verwenden firmenspezifische Hard- und Software zur Kommunikation. Zur Installation müssen je nach Sensor spezielle und teure Baugruppen in der Steuerung eingesetzt werden. Die heterogene Verdrahtung mit den unterschiedlichsten Leitungstypen und Anschlussbelegungen führt zu einem hohen Installationsaufwand. Um die Störsicherheit sowohl der analogen als auch der digitalen Signale sicherzustellen, sind abschirmtechnisch hohe Maßnahmen notwendig. In der Praxis zeigt sich immer wieder, dass Störungen bei der Signalübertragung häufig auf eine fehlerhafte oder nicht ausreichende Abschirmung zurückzuführen sind. Auch die Vernetzung und Einbindung der diversen Schnittstellen und Übertragungsprotokolle ist aufwendig und fehleranfällig. Bei einer Maschinenumstellung, bei einem Austausch oder bei einer Überprüfung der Geräte müssen die Parameter manuell am Gerät oder über ein separates Tool direkt für jeden Sensor und Aktor eingestellt werden. Wie sich immer wieder zeigt, ist dies eine wesentliche Fehler- und Manipulationsquelle für den sicheren Betrieb der Anlagen. Da es keine durchgängige Kommunikation von der Feldgeräteebene mit den überlagerten Ebenen gibt, stehen Diagnosedaten der Sensoren und Aktoren nicht zur Verfügung. Doch oft sind es gerade diese Baugruppen, die aufgrund ihrer Positionierung in der Anlage und dem Einsatz unter schwierigen industriellen Produktionsbedingungen wie Wärme, Kälte, Vibration, Schmutz und Feuchtigkeit als Fehlerquelle für Anlagenstillstände verantwortlich sind. Ohne Diagnosedaten gestaltet sich eine Fehlersuche und Behebung oft als schwierig und zeitaufwendig. An eine präventive Wartung zur Vermeidung von ungeplanten Stillstandszeiten ist schon gar nicht zu denken.
Die Zukunft heißt IO-Link
Ein derart breit gefächertes Angebot an Bussystemen und das Fehlen von Standards ist für die Entwicklung der Automatisierungstechnologie eher ein großer Nachteil. Dies mussten auch die Hersteller von Automatisierungsprodukten erkennen. So haben sich die führenden Anbieter zu einem Konsortium zusammengeschlossen mit der Zielsetzung, eine allgemein gültige und weltweit standardisierte I/O-Schnittstellentechnologie für die Kommunikation von Sensoren und Aktoren zu entwickeln. Entstanden ist das IO-Link Konzept zur einheitlichen, feldbusunabhängigen und herstellerübergreifenden Anbindung von Schaltgeräten und Sensoren an die Steuerungsebene mittels einer kostengünstigen Punkt-zu-Punkt Verbindung. Dieser Kommunikationsstandard ist in der IEC 61131-9 Norm definiert. IO-Link Devices schaffen die Transparenz und durchgehende Kommunikation von der Feldgeräteebene bis hin zur obersten Automatisierungsebene (Bild 2). Als offene Schnittstelle lässt sich IO-Link in alle gängigen Feldbus- und Automatisierungssysteme integrieren. Mit IO-Link soll letztendlich statt der bisherigen parallelen Nutzung von analogen, schaltenden und digitalen Signalen ausschließlich die digitale Übertragung zum Einsatz kommen. IO-Link bietet die Möglichkeit einer zentralen Fehlerdiagnose und –lokalisierung bis zur Aktor-/Sensorebene. Durch die Möglichkeit der dynamischen Parametrierung der Sensoren aus der Anlagensteuerung heraus können die Feldgeräte während des Betriebes auf die jeweiligen Produktionserfordernisse eingestellt werden. Feldgeräte mit IO-Link Schnittstelle bilden somit die Grundlage für die Umsetzung der Industrie 4.0.
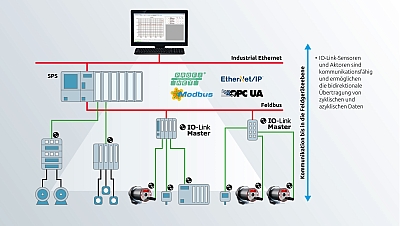
Abb. 2 IO-Link ermöglicht die durchgängige Kommunikation bis in die Ebene der Feldgeräte.
Vorteile der IO-Link-Schnittstelle
Die IO-Link Schnittstelle wird sicherlich zu Recht als die USB-Schnittstelle der Automatisierungstechnik bezeichnet. Beides sind kostengünstige serielle Punkt-zu-Punkt Verbindungen für die Signalübertragung und eignen sich für den Plug-and-Play Betrieb. Ein wesentliches Merkmal ist die sehr einfache Verdrahtung mittels standardisierten Leitungen mit schraubbarem Steckeranschluss. Neben der enormen Zeiteinsparung bei der Verdrahtung durch das Entfallen von Klemmleisten, vermeidet die Steckerlösung die Fehlerquelle einer falschen und unsachgemäßen Verbindung. Durch das Wegfallen von separaten Multipolkabeln für die analoge Signalübertragung, den Schaltkontakt und die externe Parametrierung reduziert sich der Verdrahtungsaufwand als auch der Platzbedarf im Schaltschrank, da nicht mehr jedes Gerät separat an die zentrale Peripherie angeschlossen werden brauch. Die herstellerübergreifende Standardisierung reduziert die Schnittstellenvielfalt von Sensoren und IO-Baugruppen sowie die unterschiedlichen Verbindungsleitungen.
Sensoren mit einer IO-Link Schnittstelle bieten eine zuverlässige Diagnosemöglichkeit. Diagnosemeldungen insbesondere auch präventive Zustandsmeldungen können inklusive der Beschreibung weiter geleitet und am HMI (Human Maschine Interface) angezeigt werden. Somit kann bei einem Sensorausfall, einer Verschmutzung bei optischen Sensoren, einer unzulässigen Betriebstemperatur, beim Drahtbruch oder Kurzschluss schnell reagiert und längere Stillstandszeiten vermieden werden.
Wird dennoch ein Austausch eines Sensors notwendig, steckt bisher eine große Fehlerquelle in der korrekten Parametrierung oder sogar in dem Einsatz eines falschen Sensors. Bei IO-Link Geräten sind die Parameter in dem IO-Link Master gespeichert. Mit IO-Link findet eine Geräteidentifikation durch die eindeutige Seriennummern, Vendor- und Device ID statt, was eine Verwechselung von Geräten ausschließt. Bei einem Tausch eines Gerätes werden zudem die Parameter automatisch zum Sensor übertragen. Eine Fehlbedienung oder sogar Manipulation ist damit ausgeschlossen. Zudem lassen sich die Parameteränderungen dokumentieren und damit später nachverfolgen.
Die IO-Link Datenübertragung basiert auf einem 24 V Signal und ist deshalb besonders unempfindlich gegenüber elektromagnetischen Störungen. Da die Signalübertragung rein digital und abgesichert mittels Checksummen erfolgt, sind fehlerhafte Übertragungen und Ungenauigkeiten durch die Signalumwandlungen wie bei Analogsignalen ausgeschlossen. Abgeschirmte Leitungen und gesonderte Erdungsmaßnahmen sind in der Regel nicht erforderlich.
Sensoren mit einer IO-Link Schnittstelle bieten eine zuverlässige Diagnosemöglichkeit. Diagnosemeldungen insbesondere auch präventive Zustandsmeldungen können inklusive der Beschreibung weiter geleitet und am HMI (Human Maschine Interface) angezeigt werden. Somit kann bei einem Sensorausfall, einer Verschmutzung bei optischen Sensoren, einer unzulässigen Betriebstemperatur, beim Drahtbruch oder Kurzschluss schnell reagiert und längere Stillstandszeiten vermieden werden.
Wird dennoch ein Austausch eines Sensors notwendig, steckt bisher eine große Fehlerquelle in der korrekten Parametrierung oder sogar in dem Einsatz eines falschen Sensors. Bei IO-Link Geräten sind die Parameter in dem IO-Link Master gespeichert. Mit IO-Link findet eine Geräteidentifikation durch die eindeutige Seriennummern, Vendor- und Device ID statt, was eine Verwechselung von Geräten ausschließt. Bei einem Tausch eines Gerätes werden zudem die Parameter automatisch zum Sensor übertragen. Eine Fehlbedienung oder sogar Manipulation ist damit ausgeschlossen. Zudem lassen sich die Parameteränderungen dokumentieren und damit später nachverfolgen.
Die IO-Link Datenübertragung basiert auf einem 24 V Signal und ist deshalb besonders unempfindlich gegenüber elektromagnetischen Störungen. Da die Signalübertragung rein digital und abgesichert mittels Checksummen erfolgt, sind fehlerhafte Übertragungen und Ungenauigkeiten durch die Signalumwandlungen wie bei Analogsignalen ausgeschlossen. Abgeschirmte Leitungen und gesonderte Erdungsmaßnahmen sind in der Regel nicht erforderlich.
Komponenten des IO-Link-Systems
Ein IO-Link System besteht aus IO-Link Mastern als Gateway zwischen dem übergeordneten Kommunikationssystemen wie Profinet, Ethernet/IP und den IO-Link Devices. Die IO-Link Devices sind dabei die kommunikationsfähigen Feldgeräte wie beispielsweise Sensoren, Schaltgeräte, Ventile oder Signalleuchten.
Die Datenübertragung per IO-Link erfolgt grundsätzlich zwischen einem IO-Link Master und dem IO-Link Device als Slave. Als IO-Link Master stehen sowohl Feldbus-Anschaltbaugruppen als auch SPS-Schnittstellenbaugruppen zur Verfügung. Wahlweise lassen sich schaltende Geräte wie bisher wie ein Schalteingang oder Schaltausgang betreiben oder aber in der Betriebsart IO-Link der Schaltzustand digital übertragen. Da beide Signale über denselben Pin 4 übertragen werden, ist ein Parallelbetrieb ausgeschlossen. In einem IO-Link System können Komponenten mit und ohne IO-Link beliebig kombiniert und parallel betrieben werden. Nicht IO-Link fähige Standardgeräte können entweder über spezielle Standard-IO-Ports oder über die kompatiblen IO-Link-Ports des Masters angeschlossen werden. Binäre oder analoge Sensoren können so über den Master mit der Feldbusebene verknüpft werden. Die Abwärtskompatibilität der IO-Link-Ports wird von der IO-Link-Anschaltbaugruppe durch zwei unterschiedliche Betriebsmodi dem IO-Link Modus und dem Standard-IO-Modus (SIO) sichergestellt. IO-Link Sensoren können wie ein binäres Gerät betrieben werden. Somit kann ein IO-Link Schaltsensor auch in klassischen Automatisierungslösungen integriert werden. Bei der Initialisierung baut der IO-Link Master automatisch eine Kommunikation auf. Ein gemischter Betrieb von Standard-Sensoren und IO-Link Sensoren wird durch den IO-Link Standard unterstützt.
Bei IO-Link wird die Leitung für das Schaltsignal gleichzeitig für die serielle Kommunikation genutzt. Technisch handelt es sich um eine Halbduplex-Schnittstelle, bei der das Senden und Empfangen von Daten nacheinander erfolgt. Standardmäßig werden M12-Stecker eingesetzt. Die maximale Kabellänge bis zum IO-Link Master beträgt 20 m.
Die Datenübertragung per IO-Link erfolgt grundsätzlich zwischen einem IO-Link Master und dem IO-Link Device als Slave. Als IO-Link Master stehen sowohl Feldbus-Anschaltbaugruppen als auch SPS-Schnittstellenbaugruppen zur Verfügung. Wahlweise lassen sich schaltende Geräte wie bisher wie ein Schalteingang oder Schaltausgang betreiben oder aber in der Betriebsart IO-Link der Schaltzustand digital übertragen. Da beide Signale über denselben Pin 4 übertragen werden, ist ein Parallelbetrieb ausgeschlossen. In einem IO-Link System können Komponenten mit und ohne IO-Link beliebig kombiniert und parallel betrieben werden. Nicht IO-Link fähige Standardgeräte können entweder über spezielle Standard-IO-Ports oder über die kompatiblen IO-Link-Ports des Masters angeschlossen werden. Binäre oder analoge Sensoren können so über den Master mit der Feldbusebene verknüpft werden. Die Abwärtskompatibilität der IO-Link-Ports wird von der IO-Link-Anschaltbaugruppe durch zwei unterschiedliche Betriebsmodi dem IO-Link Modus und dem Standard-IO-Modus (SIO) sichergestellt. IO-Link Sensoren können wie ein binäres Gerät betrieben werden. Somit kann ein IO-Link Schaltsensor auch in klassischen Automatisierungslösungen integriert werden. Bei der Initialisierung baut der IO-Link Master automatisch eine Kommunikation auf. Ein gemischter Betrieb von Standard-Sensoren und IO-Link Sensoren wird durch den IO-Link Standard unterstützt.
Bei IO-Link wird die Leitung für das Schaltsignal gleichzeitig für die serielle Kommunikation genutzt. Technisch handelt es sich um eine Halbduplex-Schnittstelle, bei der das Senden und Empfangen von Daten nacheinander erfolgt. Standardmäßig werden M12-Stecker eingesetzt. Die maximale Kabellänge bis zum IO-Link Master beträgt 20 m.
In der ersten Konzeptphase zur Spezifikation der IO-Link Schnittstelle lag der Fokus auf schaltende Sensoren und Aktoren. Inzwischen wurde erkannt, dass die Verwendung der IO-Link Schnittstelle auch für messende Geräte sinnvoll ist. Mehr und mehr Sensorhersteller bieten dazu bereits Geräte für diverse physikalische Messgrößen an. In der IO-Link Spezifikation sind gemäß der Anschlussbelegung Port Class A nur die Pins 1,3 und 4 fest definiert. Pin 2 und 5, die bei Bedarf für eine zusätzliche Spannungsversorgung bei erhöhtem Strombedarf verwendet werden, können bei den messenden Geräten alternativ für den Analogausgang 0/4-20 mA oder für einen zweiten Schaltausgang verwendet werden (Bild 3).
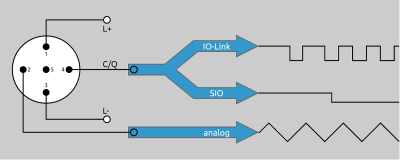
Abb. 3 Anschluss eines modernen Sensors mit IO-Link Schnittstelle und Analogausgang.
Solange die Anwender noch nicht auf den Analogausgang komplett verzichten möchten, ergeben sich durch den Parallelbetrieb des Analogausganges, Schaltausganges und der digitalen Schnittstelle interessante Möglichkeiten der externen Parametrierung, Auswertung von Störmeldungen und Diagnosesignalfunktionen. Wenn später die Steuerung auf eine rein digitale Messwertübertragung umgestellt wird, beschränkt sich der Aufwand lediglich auf die Konfigurationsänderung der Steuerungssoftware. Messgeräte wie beispielsweise Infrarot-Thermometer zur berührungslosen Temperaturmessung müssen kleinste Signale im Pico-Amperbereich verarbeiten. Dies verlangt ein hohes Maß an internen Störsicherheitsmaßnahmen als auch externen Maßnahmen wie die Verwendung einer abgeschirmten Leitung. Zwar wirbt das IO-Link Konsortium damit, dass für den Anschluss von IO-Link Devices keine abgeschirmte Leitung notwendig ist, da sich digitale Signale nicht stören lassen. Mit der Einführung der IO-Link Schnittstelle bei den messenden Geräten sind hier gewisse Einschränkungen unumgänglich. Der Markt hat auch schon darauf reagiert und bietet konfektionierte Leitungen mit Abschirmung an.
Datenarten der IO-Link-Kommunikation
Die IO-Link Kommunikation unterstützt die Übertragung von zyklischen und azyklischen Daten. Prozessdaten und Statusinformationen über die Gültigkeit der Prozessdaten werden zyklisch übertragen. Gerätedaten wie Identifikationsdaten, Parameter und Diagnoseinformationen werden azyklisch auf Anforderung des IO-Link Masters ausgetauscht. Des Weiteren werden von einem Device Ereignisse wie Fehlermeldungen (Kurzschluss, Unterbrechung) oder Warnmeldungen (Verschmutzung, Überhitzung) an den Master gemeldet.
Einbindung von IO-Link-Geräten in die Steuerung
Um die Zugriffe des Anwenderprogramms der Steuerung auf die Devices zu vereinheitlichen, sind für IO-Link Geräteprofile definiert. Darin sind die Datenstruktur, die Dateninhalte und die Basisfunktionalität festgeschrieben. Damit wird ein identischer Programmzugriff der Steuerung erreicht. Für IO-Link ist das Geräteprofil „Smart Sensor Profil“ definiert.
Bestandteil eines IO-Link Gerätes ist die IODD (IO Device Description) sprich eine Gerätebeschreibungsdatei. Der Aufbau der IODD ist für alle Devices aller Hersteller gleich. Damit ist die gleiche Handhabung für alle IO-Link Devices herstellerunabhängig garantiert. Darin enthalten sind alle Informationen und beschreibenden Texte zur Identifikation, zu den Geräteparametern mit Wertebereichen, den Fehlermeldungen, den Prozess- und Diagnosedaten sowie den Kommunikationseigenschaften (Bild 4). Die Texte können mehrsprachig hinterlegt werden. In dem IO-Link Master werden die Ports der angeschlossenen Devices zugeordnet (Bild 5). Der IO-Link Master ist dann meist als Feldbusslave an die Steuerung angekoppelt.
Bestandteil eines IO-Link Gerätes ist die IODD (IO Device Description) sprich eine Gerätebeschreibungsdatei. Der Aufbau der IODD ist für alle Devices aller Hersteller gleich. Damit ist die gleiche Handhabung für alle IO-Link Devices herstellerunabhängig garantiert. Darin enthalten sind alle Informationen und beschreibenden Texte zur Identifikation, zu den Geräteparametern mit Wertebereichen, den Fehlermeldungen, den Prozess- und Diagnosedaten sowie den Kommunikationseigenschaften (Bild 4). Die Texte können mehrsprachig hinterlegt werden. In dem IO-Link Master werden die Ports der angeschlossenen Devices zugeordnet (Bild 5). Der IO-Link Master ist dann meist als Feldbusslave an die Steuerung angekoppelt.
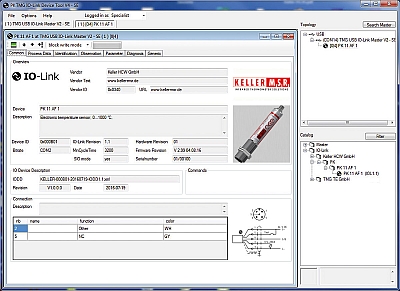
Abb. 4 Eigenschaften des angeschlossenen IO-Device.
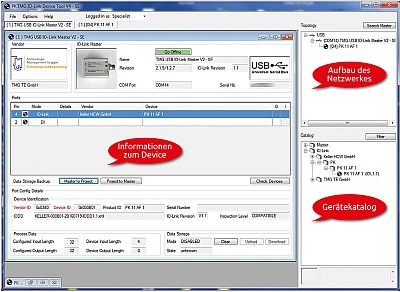
Abb. 5 Einbindung eines IO-Sensors an den Master.
Parametrierung und Diagnose erfolgen automatisch durch einen Funktionsbaustein in der Maschinensteuerung. Bei der Parametrierung werden vom Funktionsbaustein zunächst über IO-Link die Identifikationsparameter der angeschlossenen Geräte abgefragt. Anschließend wird per Datenbankvergleich geprüft, ob diese Sensoren für die Maschinen zugelassen sind. Im positiven Fall findet der Funktionsbaustein die zu den Sensoren gehörende Konfigurationsparameter ebenfalls in der Datenbank. Diese werden dann bei Bedarf via IO-Link automatisch in die jeweiligen Sensoren geschrieben. Beispielsweise lassen sich bei dem Pyrometer (Bild 6) der Emissionsgrad, die Schaltpunkte und Funktion des Schaltkontaktes, die Skalierung des Analogausganges und der Maximalwertspeicher parametrieren.
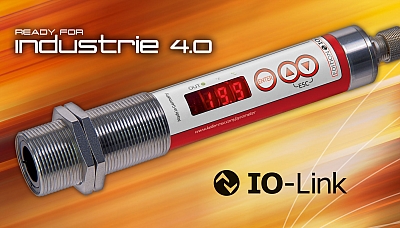
Abb. 6 Pyrometer mit IO-Link Schnittstelle, Analogausgang und Schaltkontakt.
Weiterhin sind als Kommandofunktionen eine Temperatursimulation, ein Selbsttest und das Rücksetzen auf Werkseinstellung möglich (Bild 7). Fehler in der Hard- oder Software, Wartungsaufforderungen oder der Betrieb des Gerätes außerhalb der Spezifikation lassen sich über u.a. die Diagnosefunktion auswerten. Mit der Einbindung in die Steuerung werden die Sensoren auch für eine Fernwartung zugänglich.
Die anwenderspezifische Parametrierung eines IO-Link Gerätes kann extern auf drei Arten erfolgen: über einen PC mit einem USB IO-Link-Master, über ein Software-Tool in der SPS Steuerung oder programmgesteuert durch Funktionsbausteine der Anlagensteuerung.
Die anwenderspezifische Parametrierung eines IO-Link Gerätes kann extern auf drei Arten erfolgen: über einen PC mit einem USB IO-Link-Master, über ein Software-Tool in der SPS Steuerung oder programmgesteuert durch Funktionsbausteine der Anlagensteuerung.
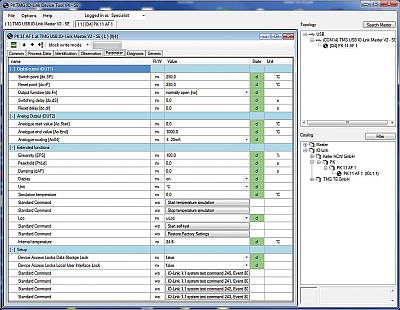
Abb. 7 Einstellung der Parameter und Kommandos.
IO-Link Tools für den Service
Ein alt eingesessener Inbetriebnehmer wird sicherlich argumentieren, dass es bisher viel einfacher war, einen analogen Sensor mittels Stommessgerätel zu überprüfen. Die Parametrierung konnte über Taster oder Schalter am Gerät eingestellt werden. Wenn man dann jedoch auf die sonstigen Vorzüge der digitalen Kommunikation verzichten muss stellt sich die Frage, ob dies heute wirklich im internationalen Wettbewerb zur Optimierung der Produktionskosten noch ein kaufentscheidendes Argument sein kann.
Für den Service werden IO-Link USB-Master angeboten (Bild 8). Damit lässt sich ein IO-Link Device über einen PC per USB-Schnittstelle betreiben. Spezielle IO-Link Adapter können in die Zuleitung eingeschliffen werden, um rückwirkungsfrei kabelgebunden oder auch drahtlos per Bluetooth auf die Daten zugreifen und aufzeichnen zu können. Auch stehen Adapter zum Klonen der Geräteparameter zur Verfügung.
Für den Service werden IO-Link USB-Master angeboten (Bild 8). Damit lässt sich ein IO-Link Device über einen PC per USB-Schnittstelle betreiben. Spezielle IO-Link Adapter können in die Zuleitung eingeschliffen werden, um rückwirkungsfrei kabelgebunden oder auch drahtlos per Bluetooth auf die Daten zugreifen und aufzeichnen zu können. Auch stehen Adapter zum Klonen der Geräteparameter zur Verfügung.
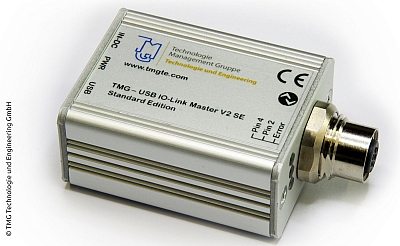
Abb. 8 IO-Link Master zum Anschluss eines IO-Link Device über die USB-Schnittstelle an einen PC.
Wie schnell sich die Umstellung auf die rein digitale Signalkommunikation vollziehen wird, ist nicht vorhersehbar und sicherlich eng vom Automatisierungsgrad der Maschinen, der Industrie und den Anwendungen abhängig. Da moderne-Sensoren mit IO-Link Schnittstelle und Analogausgang oft ohne Mehrpreis angeboten werden ist es empfehlenswert, bei einem Austausch, einer Anlagenerweiterung oder auch bei Neuanlage vorausschauend diese Geräte einzusetzen. Eine spätere Umstellung wird dadurch denkbar einfach und ist ohne Umrüstkosten der Sensoren und der Verdrahtung möglich.
Mittlerweile werden bereits über 3000 IO-Link Produkte angeboten. Für 16 Feldbus-Systeme sind inzwischen IO-Link Master verfügbar. Zusätzlich bieten auch schon 8 Steuerungshersteller zentrale Master an. Hinzu kommen zahlreiche Hersteller von Sensoren für die verschiedensten Messgrößen, zur Objekterkennung oder zur Positionserfassung sowie Aktoren wie Signalleuchten, Ventile, Leistungsschütze oder Frequenzumrichter. Auch bieten inzwischen diverse Firmen die Technologie zum Gerätedesign und für den technischen Support an. Durch die Zertifizierungspflicht und Verwendung von akkreditierten Testtools ist sichergestellt, dass alle am Markt erhältlichen Produkte den IO-Link Standard erfüllen.
Mittlerweile werden bereits über 3000 IO-Link Produkte angeboten. Für 16 Feldbus-Systeme sind inzwischen IO-Link Master verfügbar. Zusätzlich bieten auch schon 8 Steuerungshersteller zentrale Master an. Hinzu kommen zahlreiche Hersteller von Sensoren für die verschiedensten Messgrößen, zur Objekterkennung oder zur Positionserfassung sowie Aktoren wie Signalleuchten, Ventile, Leistungsschütze oder Frequenzumrichter. Auch bieten inzwischen diverse Firmen die Technologie zum Gerätedesign und für den technischen Support an. Durch die Zertifizierungspflicht und Verwendung von akkreditierten Testtools ist sichergestellt, dass alle am Markt erhältlichen Produkte den IO-Link Standard erfüllen.