Независимый от производителя интерфейс IO-Link для интеллектуальной автоматизации процессов
Введение
Индустрия 4.0 и инновационные концепции машин в настоящее время являются предметом широкого обсуждения в области технологий автоматизации. Интеллектуальные датчики являются основной предпосылкой для создания сквозной сети, полной прозрачности и бесперебойной связи аналоговых систем вплоть до самого низкого уровня полевых устройств. С помощью интерфейса IO-Link была создана новая, независимая от полевой шины и производителя концепция связи для стандартизированного подключения датчиков и исполнительных устройств к уровню управления посредством простого и экономически эффективного соединения "точка-точка". В следующем отчете представлена технология и применение интерфейса IO-Link.
Индустрия 4.0
Индустрия 4.0 - это объединение информационных технологий (ИТ) и телекоммуникационных технологий в ИТК. Она основана на объединении в сеть датчиков, исполнительных механизмов и обработки данных для сквозной связи вплоть до уровня полевых устройств. Концепция Индустрии 4.0 включает в себя цифровизацию, автоматизацию и объединение в сеть всех приложений для управления общим процессом для всех функций, областей и сегментов обрабатывающей промышленности, вплоть до экономической деятельности. Эта трансформация в первую очередь обусловлена растущими требованиями клиентов и необходимостью для производственных компаний быть в состоянии выполнять все более быстрые, динамичные и индивидуализированные пожелания клиентов. Это требует перехода от жестких, централизованных систем управления производством к децентрализованным интеллектуальным системам, вплоть до уровня полевых устройств.
Внедрение Индустрии 4.0 в производственные процессы призвано обеспечить адаптивное производство и оптимизацию отдельных процессов в режиме реального времени. Материалы и компоненты должны выбираться самостоятельно в соответствии с определенными технологиями производства и процесса, а также должна быть предусмотрена возможность адаптации и перенастройки в режиме реального времени в соответствии с девизом "Продукт управляет системой". Преимущества заключаются в повышении эффективности и гибкости благодаря более быстрому реагированию на большее количество вариантов, сокращении циклов переналадки для сложных изделий, производстве различных серий или отдельных изделий с помощью одной и той же системы, индивидуализации продукции с учетом пожеланий клиентов и производстве малых и очень малых серий по конкурентоспособным ценам.
Концепция Industry 4.0 предусматривает переход от профилактического обслуживания и ремонта систем к предиктивной диагностике и удаленному обслуживанию, в том числе за пределами предприятия и в разных местах. Все это требует доступа к подключенным интеллектуальным источникам данных, таким как датчики или исполнительные механизмы.
Одним из недостатков Индустрии 4.0 является частое отсутствие стандартизации и неточное определение этого термина. Межсистемная согласованность и, следовательно, глобальное использование требуют стандартизированной структуры для технологий, систем и процессов, основанной на международных нормах и стандартах. Кроме того, необходима фундаментальная стандартизация принципов структурирования, интерфейсов и форматов данных.
Внедрение Индустрии 4.0 в производственные процессы призвано обеспечить адаптивное производство и оптимизацию отдельных процессов в режиме реального времени. Материалы и компоненты должны выбираться самостоятельно в соответствии с определенными технологиями производства и процесса, а также должна быть предусмотрена возможность адаптации и перенастройки в режиме реального времени в соответствии с девизом "Продукт управляет системой". Преимущества заключаются в повышении эффективности и гибкости благодаря более быстрому реагированию на большее количество вариантов, сокращении циклов переналадки для сложных изделий, производстве различных серий или отдельных изделий с помощью одной и той же системы, индивидуализации продукции с учетом пожеланий клиентов и производстве малых и очень малых серий по конкурентоспособным ценам.
Концепция Industry 4.0 предусматривает переход от профилактического обслуживания и ремонта систем к предиктивной диагностике и удаленному обслуживанию, в том числе за пределами предприятия и в разных местах. Все это требует доступа к подключенным интеллектуальным источникам данных, таким как датчики или исполнительные механизмы.
Одним из недостатков Индустрии 4.0 является частое отсутствие стандартизации и неточное определение этого термина. Межсистемная согласованность и, следовательно, глобальное использование требуют стандартизированной структуры для технологий, систем и процессов, основанной на международных нормах и стандартах. Кроме того, необходима фундаментальная стандартизация принципов структурирования, интерфейсов и форматов данных.
Пределы классической технологии автоматизации
Предыдущие системы сетевого взаимодействия и полевых шин были разработаны ведущими производителями ПЛК, которые поддерживают специфические для системы технологии и оптимально адаптированы к их инструментам программирования и конфигурирования. На рынке существует несколько конкурирующих систем, таких как Profibus/ProfiNet (Siemens), DeviceNet и ControlNet (Rockwell Automation), Modbus и CANopen (Schneider Electric), Interbus (Phoenix Contact) или CC-Link (Mitsubishi Electric). Тип используемого ПЛК определяет, какая полевая шина используется. Существуют значительные технические различия в длине кабеля, количестве битов данных и наборе функций. Дополнительные функции, такие как диагностика, ациклическая передача данных по запросу, обработка аварийных сигналов и перекрестный трафик между отдельными узлами шины, поддерживаются не всеми системами полевых шин.
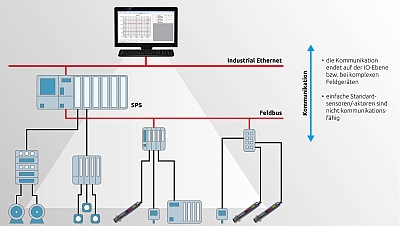
Abb. 1 Классическая система автоматизации с ограниченными возможностями связи.
В классической технологии автоматизации связь до сих пор осуществлялась на самом нижнем уровне полевой шины, то есть на уровне датчиков и исполнительных механизмов (рис. 1). Во многих случаях там используются модули без коммуникационных возможностей, которые ограничиваются чисто аналоговыми или коммутационными входными и выходными сигналами. Имеющиеся на рынке датчики и исполнительные устройства с цифровым интерфейсом не стандартизированы, а используют для связи аппаратное и программное обеспечение, специфичное для конкретной компании. В зависимости от датчика для установки в систему управления необходимо использовать специальные и дорогостоящие модули. Неоднородная проводка с большим разнообразием типов кабелей и назначений контактов приводит к высоким затратам на установку. Для обеспечения помехоустойчивости как аналоговых, так и цифровых сигналов необходимы высокие меры экранирования. На практике неоднократно доказывалось, что помехи при передаче сигналов часто возникают из-за дефектов или недостаточного экранирования. Объединение в сеть и интеграция различных интерфейсов и протоколов передачи также сложны и чреваты ошибками. В случае переналадки оборудования, замены или проверки устройств параметры должны быть установлены вручную на устройстве или непосредственно для каждого датчика и исполнительного механизма с помощью отдельного инструмента. Как было неоднократно показано, это является основным источником ошибок и манипуляций, мешающих безопасной эксплуатации систем. Поскольку нет непрерывной связи от уровня полевого устройства до более высоких уровней, диагностические данные от датчиков и исполнительных механизмов недоступны. Однако именно эти узлы часто становятся причиной простоев системы из-за их расположения в системе и использования в сложных условиях промышленного производства, таких как жара, холод, вибрация, грязь и влага. Без диагностических данных поиск и устранение неисправностей зачастую затруднены и занимают много времени. О профилактическом обслуживании во избежание незапланированных простоев даже не может быть и речи.
Будущее называется IO-Link
Такой широкий спектр шинных систем и отсутствие стандартов - это серьезный недостаток для развития технологий автоматизации. Это вынуждены были признать и производители средств автоматизации. Поэтому ведущие поставщики создали консорциум с целью разработки общеприменимой и стандартизированной во всем мире технологии интерфейса ввода-вывода для связи датчиков и исполнительных механизмов. Результатом стала концепция IO-Link для стандартизированного, независимого от полевой шины и производителя подключения коммутационных устройств и датчиков к уровню управления с помощью экономически эффективного соединения "точка-точка". Этот стандарт связи определен в стандарте IEC 61131-9. Устройства IO-Link обеспечивают прозрачность и непрерывную связь от уровня полевых устройств до самого высокого уровня автоматизации (рис. 2). Будучи открытым интерфейсом, IO-Link может быть интегрирован во все распространенные полевые шины и системы автоматизации. С IO-Link в конечном итоге будет использоваться только цифровая передача данных вместо прежнего параллельного использования аналоговых, коммутационных и цифровых сигналов. IO-Link предоставляет возможность централизованной диагностики и локализации неисправностей вплоть до уровня привода/датчика. Благодаря возможности динамической параметризации датчиков из системы управления, полевые устройства могут быть настроены на соответствующие производственные требования в процессе эксплуатации. Таким образом, полевые устройства с интерфейсом IO-Link являются основой для внедрения Индустрии 4.0.
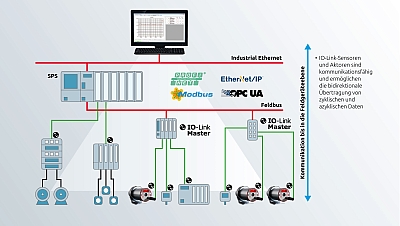
Abb. 2 IO-Link обеспечивает непрерывную связь вплоть до уровня полевого устройства.
Преимущества интерфейса IO-Link
Интерфейс IO-Link, безусловно, справедливо называют интерфейсом USB в технологии автоматизации. Оба они представляют собой экономически эффективные последовательные соединения "точка-точка" для передачи сигналов и подходят для работы по принципу "подключи и работай". Ключевой особенностью является очень простое подключение с помощью стандартизированных кабелей с винтовыми штекерами. Помимо огромной экономии времени на прокладку кабелей за счет отказа от клеммных колодок, решение с разъемами позволяет избежать ошибок при неправильном подключении. Отказ от отдельных многоконтактных штекерных кабелей для передачи аналогового сигнала, переключающего контакта и внешней параметризации снижает трудоемкость проводки, а также уменьшает занимаемое пространство в шкафу управления, поскольку каждое устройство больше не нужно подключать отдельно к центральной периферии. Независимая от производителя стандартизация сокращает разнообразие интерфейсов для датчиков и модулей ввода-вывода, а также различных соединительных кабелей.
Датчики с интерфейсом IO-Link обеспечивают надежную возможность диагностики. Диагностические сообщения, особенно профилактические сообщения о состоянии, могут передаваться с описанием и отображаться на HMI (человеко-машинном интерфейсе). Это означает, что в случае отказа датчика, загрязнения в случае оптических датчиков, недопустимой рабочей температуры, обрыва провода или короткого замыкания можно быстро отреагировать и избежать длительных простоев.
Если датчик все же необходимо заменить, основным источником ошибок до сих пор была правильная параметризация или даже использование неправильного датчика. В устройствах IO-Link параметры хранятся в памяти ведущего устройства IO-Link. Устройства IO-Link идентифицируются по уникальному серийному номеру, идентификатору производителя и устройства, что предотвращает перепутывание устройств. При замене устройства параметры также автоматически переносятся в датчик. Это предотвращает неправильную работу или даже манипуляции. Изменения параметров также могут быть задокументированы и, таким образом, отслежены позднее.
Передача данных IO-Link основана на сигнале 24 В и поэтому особенно нечувствительна к электромагнитным помехам. Поскольку передача сигнала осуществляется исключительно в цифровом виде и защищена контрольными суммами, исключены сбои в передаче и неточности, связанные с преобразованием сигнала, как в случае с аналоговыми сигналами. Экранированные кабели и отдельное заземление, как правило, не требуются.
Датчики с интерфейсом IO-Link обеспечивают надежную возможность диагностики. Диагностические сообщения, особенно профилактические сообщения о состоянии, могут передаваться с описанием и отображаться на HMI (человеко-машинном интерфейсе). Это означает, что в случае отказа датчика, загрязнения в случае оптических датчиков, недопустимой рабочей температуры, обрыва провода или короткого замыкания можно быстро отреагировать и избежать длительных простоев.
Если датчик все же необходимо заменить, основным источником ошибок до сих пор была правильная параметризация или даже использование неправильного датчика. В устройствах IO-Link параметры хранятся в памяти ведущего устройства IO-Link. Устройства IO-Link идентифицируются по уникальному серийному номеру, идентификатору производителя и устройства, что предотвращает перепутывание устройств. При замене устройства параметры также автоматически переносятся в датчик. Это предотвращает неправильную работу или даже манипуляции. Изменения параметров также могут быть задокументированы и, таким образом, отслежены позднее.
Передача данных IO-Link основана на сигнале 24 В и поэтому особенно нечувствительна к электромагнитным помехам. Поскольку передача сигнала осуществляется исключительно в цифровом виде и защищена контрольными суммами, исключены сбои в передаче и неточности, связанные с преобразованием сигнала, как в случае с аналоговыми сигналами. Экранированные кабели и отдельное заземление, как правило, не требуются.
Компоненты системы IO-Link
Система IO-Link состоит из IO-Link-мастеров, являющихся шлюзом между коммуникационными системами более высокого уровня, такими как Profinet, Ethernet/IP, и IO-Link-устройствами. Устройства IO-Link - это полевые устройства с коммуникационными возможностями, такие как датчики, коммутационные устройства, клапаны или сигнальные лампы.
Передача данных через IO-Link всегда осуществляется между ведущим устройством IO-Link и устройством IO-Link в качестве ведомого. В качестве ведущего устройства IO-Link могут использоваться как интерфейсные модули полевой шины, так и интерфейсные модули ПЛК. Коммутационные устройства могут работать как раньше, как переключающий вход или переключающий выход, или состояние переключения может передаваться в цифровом виде в режиме работы IO-Link. Поскольку оба сигнала передаются через один и тот же контакт 4, параллельная работа невозможна. В системе IO-Link компоненты с IO-Link и без него могут быть объединены и работать параллельно по мере необходимости. Стандартные устройства, не поддерживающие IO-Link, могут подключаться либо через специальные стандартные порты IO, либо через совместимые порты IO-Link ведущего устройства. Таким образом, двоичные или аналоговые датчики могут быть подключены к полевой шине через ведущее устройство. Совместимость портов IO-Link по нисходящей линии обеспечивается интерфейсным модулем IO-Link за счет двух различных режимов работы - режима IO-Link и стандартного режима IO (SIO). Датчики IO-Link могут работать как двоичные устройства. Это означает, что датчик-переключатель IO-Link может быть интегрирован в классические решения по автоматизации. При инициализации ведущий IO-Link автоматически устанавливает связь. Смешанная работа стандартных датчиков и датчиков IO-Link поддерживается стандартом IO-Link.
В IO-Link линия для коммутационного сигнала также используется для последовательной связи. Технически это полудуплексный интерфейс, в котором данные отправляются и принимаются последовательно. Стандартно используются разъемы M12. Максимальная длина кабеля до ведущего устройства IO-Link составляет 20 метров.
Передача данных через IO-Link всегда осуществляется между ведущим устройством IO-Link и устройством IO-Link в качестве ведомого. В качестве ведущего устройства IO-Link могут использоваться как интерфейсные модули полевой шины, так и интерфейсные модули ПЛК. Коммутационные устройства могут работать как раньше, как переключающий вход или переключающий выход, или состояние переключения может передаваться в цифровом виде в режиме работы IO-Link. Поскольку оба сигнала передаются через один и тот же контакт 4, параллельная работа невозможна. В системе IO-Link компоненты с IO-Link и без него могут быть объединены и работать параллельно по мере необходимости. Стандартные устройства, не поддерживающие IO-Link, могут подключаться либо через специальные стандартные порты IO, либо через совместимые порты IO-Link ведущего устройства. Таким образом, двоичные или аналоговые датчики могут быть подключены к полевой шине через ведущее устройство. Совместимость портов IO-Link по нисходящей линии обеспечивается интерфейсным модулем IO-Link за счет двух различных режимов работы - режима IO-Link и стандартного режима IO (SIO). Датчики IO-Link могут работать как двоичные устройства. Это означает, что датчик-переключатель IO-Link может быть интегрирован в классические решения по автоматизации. При инициализации ведущий IO-Link автоматически устанавливает связь. Смешанная работа стандартных датчиков и датчиков IO-Link поддерживается стандартом IO-Link.
В IO-Link линия для коммутационного сигнала также используется для последовательной связи. Технически это полудуплексный интерфейс, в котором данные отправляются и принимаются последовательно. Стандартно используются разъемы M12. Максимальная длина кабеля до ведущего устройства IO-Link составляет 20 метров.
На начальном этапе разработки концепции интерфейса IO-Link основное внимание уделялось коммутации датчиков и исполнительных механизмов. В то же время было признано, что использование интерфейса IO-Link имеет смысл и для измерительных устройств. Все больше производителей датчиков уже предлагают устройства для измерения различных физических величин. В спецификации IO-Link только контакты 1, 3 и 4 постоянно определены в соответствии с назначением контактов порта класса A. Штырьки 2 и 5, которые используются для дополнительного питания в случае повышенных требований к току, могут также использоваться для аналогового выхода 0/4-20 мА или для второго переключающего выхода на измерительных устройствах (рис. 3).
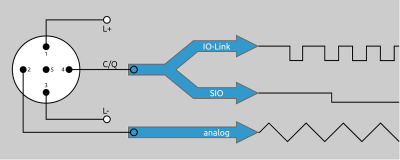
Fig. 3 Подключение современного датчика с интерфейсом IO-Link и аналоговым выходом.
Если пользователь не хочет полностью отказаться от аналогового выхода, то параллельная работа аналогового выхода, коммутационного выхода и цифрового интерфейса открывает интересные возможности для внешней параметризации, оценки сообщений о неисправностях и функций диагностических сигналов. Если впоследствии система управления будет переведена на чисто цифровую передачу измеренных значений, все усилия сводятся к изменению конфигурации управляющего программного обеспечения. Измерительные устройства, такие как инфракрасные термометры для бесконтактного измерения температуры, должны обрабатывать самые малые сигналы в пикоамперном диапазоне. Это требует высокой степени внутренней помехоустойчивости, а также внешних мер, таких как использование экранированного кабеля. Консорциум IO-Link рекламирует тот факт, что для подключения устройств IO-Link не требуется экранированный кабель, поскольку цифровые сигналы не подвержены помехам. С внедрением интерфейса IO-Link для измерительных приборов неизбежны некоторые ограничения. Рынок уже отреагировал на это и предлагает готовые кабели с экранированием.
Типы данных при обмене данными IO-Link
Коммуникация IO-Link поддерживает передачу циклических и ациклических данных. Данные процесса и статусная информация о достоверности данных процесса передаются циклически. Данные устройства, такие как идентификационные данные, параметры и диагностическая информация, передаются ациклически по запросу ведущего устройства IO-Link. Кроме того, устройство сигнализирует ведущему о таких событиях, как сообщения об ошибках (короткое замыкание, обрыв) или предупреждающие сообщения (загрязнение, перегрев).
Интеграция устройств IO-Link в систему управления
Профили устройств определяются для IO-Link с целью стандартизации доступа к устройствам со стороны пользовательской программы системы управления. Структура данных, содержание данных и базовая функциональность определены в этих профилях. Это обеспечивает идентичный доступ программы к контроллеру. Профиль устройства "Smart Sensor Profile" определен для IO-Link.
Частью устройства IO-Link является IODD (IO Device Description), т.е. файл описания устройства. Структура IODD одинакова для всех устройств всех производителей. Это гарантирует одинаковое обращение со всеми устройствами IO-Link, независимо от производителя. Он содержит всю информацию и описательные тексты для идентификации, параметры устройства с диапазонами значений, сообщения об ошибках, данные процесса и диагностики, а также коммуникационные свойства (рис. 4). Тексты могут быть сохранены на нескольких языках. Порты подключенных устройств назначаются в IO-Link-мастере (рис. 5). Ведущее устройство IO-Link обычно подключается к системе управления как ведомое устройство полевой шины.
Частью устройства IO-Link является IODD (IO Device Description), т.е. файл описания устройства. Структура IODD одинакова для всех устройств всех производителей. Это гарантирует одинаковое обращение со всеми устройствами IO-Link, независимо от производителя. Он содержит всю информацию и описательные тексты для идентификации, параметры устройства с диапазонами значений, сообщения об ошибках, данные процесса и диагностики, а также коммуникационные свойства (рис. 4). Тексты могут быть сохранены на нескольких языках. Порты подключенных устройств назначаются в IO-Link-мастере (рис. 5). Ведущее устройство IO-Link обычно подключается к системе управления как ведомое устройство полевой шины.
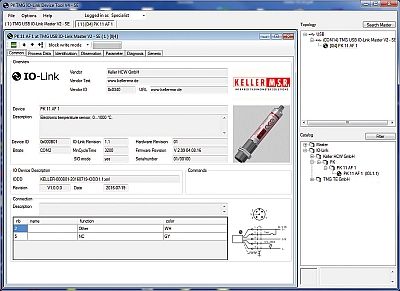
Рис. 4 Свойства подключенного IO-устройства.
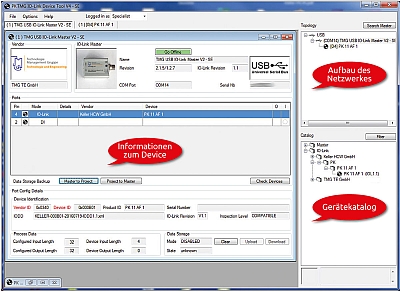
Fig. 5 Интеграция датчика IO в мастер.
Параметрирование и диагностика выполняются автоматически с помощью функционального блока в блоке управления машины. При параметрировании функциональный блок сначала запрашивает идентификационные параметры подключенных устройств через IO-Link. Затем с помощью сравнения с базой данных проверяется, авторизованы ли эти датчики для машин. Если это так, то функциональный блок также находит в базе данных параметры конфигурации, связанные с датчиками. При необходимости они автоматически записываются в соответствующие датчики через IO-Link. Например, для пирометра можно задать излучательную способность, точки переключения и функцию переключающего контакта, масштаб аналогового выхода и память максимальных значений (рис. 6).
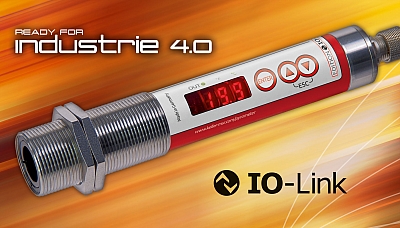
Abb. 6 Пирометр с интерфейсом IO-Link, аналоговым выходом и переключающим контактом.
Моделирование температуры, самодиагностика и возврат к заводским настройкам также возможны в качестве командных функций (рис. 7). Ошибки в аппаратном или программном обеспечении, запросы на техническое обслуживание или работа устройства вне спецификации могут быть проанализированы, в частности, с помощью функции диагностики. Интеграция в систему управления также делает датчики доступными для удаленного обслуживания.
Пользовательская параметризация устройства IO-Link может быть осуществлена извне тремя способами: через ПК с USB-ведущим IO-Link, через программное обеспечение в контроллере ПЛК или программно с помощью функциональных блоков в системном контроллере.
Пользовательская параметризация устройства IO-Link может быть осуществлена извне тремя способами: через ПК с USB-ведущим IO-Link, через программное обеспечение в контроллере ПЛК или программно с помощью функциональных блоков в системном контроллере.
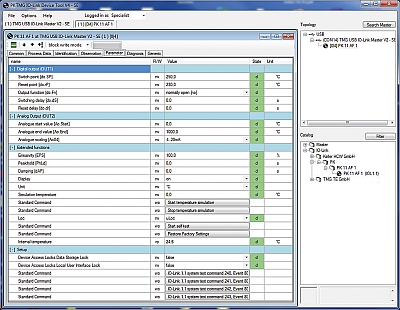
Abb. 7 Установка параметров и команд.
Инструменты IO-Link для обслуживания
Инженер-наладчик со стажем наверняка скажет, что раньше было гораздо проще проверить аналоговый датчик с помощью прибора для измерения тока. Параметризацию можно было задать с помощью кнопок или переключателей на приборе. Однако если при этом вы лишаетесь других преимуществ цифровой связи, возникает вопрос, действительно ли это может быть решающим аргументом при покупке в условиях современной международной конкуренции за оптимизацию производственных затрат.
Для обслуживания доступны USB-мастера IO-Link (рис. 8). Это позволяет управлять устройством IO-Link через ПК с помощью интерфейса USB. Специальные адаптеры IO-Link могут быть подключены к линии питания для доступа и записи данных без обратной связи, как проводной, так и беспроводной через Bluetooth. Также имеются адаптеры для клонирования параметров устройства.
Для обслуживания доступны USB-мастера IO-Link (рис. 8). Это позволяет управлять устройством IO-Link через ПК с помощью интерфейса USB. Специальные адаптеры IO-Link могут быть подключены к линии питания для доступа и записи данных без обратной связи, как проводной, так и беспроводной через Bluetooth. Также имеются адаптеры для клонирования параметров устройства.
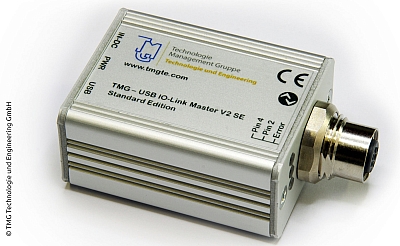
Abb. 8 IO-Link мастер для подключения устройства IO-Link к ПК через интерфейс USB.
Как быстро произойдет переход на чисто цифровую передачу сигналов, предсказать невозможно, и, конечно же, это будет зависеть от степени автоматизации оборудования, отрасли и сферы применения. Поскольку современные датчики с интерфейсом IO-Link и аналоговым выходом часто предлагаются без дополнительной оплаты, целесообразно использовать эти устройства заранее при замене или расширении системы, а также при создании новых систем. Это делает последующую замену чрезвычайно простой и возможной без каких-либо затрат на переоборудование датчиков и проводки.
В настоящее время доступно более 3000 продуктов IO-Link. Мастера IO-Link теперь доступны для 16 систем полевой шины. Кроме того, 8 производителей систем управления уже предлагают централизованные мастера. Кроме того, существует множество производителей датчиков для широкого спектра измеряемых величин, для распознавания объектов или определения положения, а также исполнительных устройств, таких как сигнальные лампы, клапаны, силовые контакторы или преобразователи частоты. В настоящее время различные компании также предлагают технологию разработки устройств и техническую поддержку. Требование сертификации и использование аккредитованных средств тестирования гарантирует, что все продукты, представленные на рынке, соответствуют стандарту IO-Link.
В настоящее время доступно более 3000 продуктов IO-Link. Мастера IO-Link теперь доступны для 16 систем полевой шины. Кроме того, 8 производителей систем управления уже предлагают централизованные мастера. Кроме того, существует множество производителей датчиков для широкого спектра измеряемых величин, для распознавания объектов или определения положения, а также исполнительных устройств, таких как сигнальные лампы, клапаны, силовые контакторы или преобразователи частоты. В настоящее время различные компании также предлагают технологию разработки устройств и техническую поддержку. Требование сертификации и использование аккредитованных средств тестирования гарантирует, что все продукты, представленные на рынке, соответствуют стандарту IO-Link.